Can anyone describe the Bullet’s airflow path? From inside the drum it’s obvious the air moves through the exhaust tube, chaff collector, filter screen, fan, and out the exhaust. But what is the path to get into the drum? I see holes in the back of the drum that must be the inlet. Does the air flow in through the chaff spill slot below the front window, around the drum?
This is partly out of curiosity, but also to understand how much pre-heating the air gets before it enters the drum. From experience with the fan speed during roasting it seems to behave as if the inlet is cold (room temperature) air, so turning up the fan cools the beans.
Here’s part of your answer…
As I understand it, air enters at the lower rear of the Bullet via the perforations at the bottom of the rear shrouds (drum motor cover & chaff collector). It’s pulled in by the cooling fan at the bottom of the rear plate (the fan is the one visible when you remove the chaff collector). How it gets from the output side of that fan to the inside of the drum is more than I know!
The gap below the exit door seems to have no significant contribution to air flow since chaff keeps falling out even at high exhaust fan settings. It’s pretty much masked by the bean mass.
So… not a complete answer but a start!
Bruce
Hi! I enjoyed this short description compliments of Dan on the Sweet Maria’s library site:
https://legacy.sweetmarias.com/library/aillio-bullet-r1-roaster-testing-airflow-with-rwanda-kegeyo/
Some of the air is preheated under the drum before entering the drum.
Thanks for the diagram! Helps a lot.
I didn’t realize the gap beneath the door was part of an intentional air path below the drum. Pre-heating that air makes sense now that you point it out. My first thought leaves me scratching my head about chaff falling out during the roast as air enters. Does that mean there’s a chance for chaff to collect below the drum? Sounds like I better make a determined effort to vacuum that better!
Bruce
Yes and chaff do accumulate, so good idea to vacuum out the front after each session.
@andyvtec The electronic fan is part of the cooling for the induction electronics. It sucks air from under the roaster, it passes the induction coil and the IGBTs to keep it all cool.
@jacob wonder if it’s possible to restrict the ambient air coming into the drum from the back to encourage more air coming through the bottom which is preheated?
By the way, have you guys tested how much air is coming from the back versus the bottom which is preheated? Like 70% back / 30% bottom preheated?
I don’t recommend modifying the airflow or blocking the air intake as it could cause overheating of other parts. The shaft and belt pulley are cooled by the back air intake.
We have not measured the exact airflow as this is technically quite difficult to accurately do.
With all due respect, is the key goal to keep the belt cooled to prevent premature aging? The shaft and pulley are metal so they should be much less susceptible to the high temperature aging. Is it correct?
If that is the case, now the goal should be either
- channeling the exhaust flow from the “electronic fan” vertically across the pully and belt assembly before the air exit the plastic housing
or - Add another fan to properly cooling the pully and belt assembly.
Both of the above solutions seem to be a lot more reasonable than sending the cooling air into the drum, to cool the shaft (which unfortunately also cools the afloat beans), so the pully and belt that thermally connected to the shaft will not be overheated. Don’t you think so?
I have done 4 roasting with the “intake” marked in the SM’s photo blocked. I see much less power needed to reach the same roasting profile. For a faster roast (1C at 6~7min) and only 400g, I was almost reaching the limit of the machine to push the RoR to where I like. Now with the modification, I can easily achieve it and the 1C temperature is also dropped down by about 10F consistently.
I am not asking Aillio to change design on Bullet, but would like to professionally discuss a possible alternative to protect the belt and reach better heating efficiency.
Thanks a lot for your reply!
I think that I got a perfect solution to my goal after I studied the exhausting air path at the back end of my bullet. Now I can achieve:
- improving the heating efficiency,
- improving convective heating
- even improving the belt and pulley life time by reducing its temperature during roast.
The solution is surprisingly simple. I just did a roasting test to confirm it. First of all, I blocked the “intake” holes marked in the above SM’s photo using the tape mod that I posted in Bullet FB page (disclaimer: you are responsible for all the consequence if you choose to do so).
Then, simply taking out the other half of the plastic enclosure that cover the motor and some electronics at the rear end. That part of casing (let’s call it “motor cover”) is simply cosmetic and may be dust/chaff proof a bit. The original exhaust air flow responsible for sucking air out of drum into the chaff collector is not affected at all. However, by removing the “motor cover” I have observed the pulley/belt temperature stay at <90F during the whole roast. If I add a small fan blowing from the motor side toward the pulley. Its temperature is about 70F. In both case, the pulley temperature is even lower that what it was in the stock form (about peak at 114F measured during roast).
I am going to 3D printed a new “motor cover” to improve the air cooling of the pulley assembly and at the same time it would allow the tape mod, which block ambient air to go into the drum and cool the beans during roast.
Can you post pics of the of the tape mod and motor cover that you removed? Also, a link to the FB post? Thanks.
If you are the member of that FB group, you can search my name, puck. There are a few posts discussing there and some Jacob’s reply. Here is one example:
Hope it help.
I think the primary reason for a faster roast is because you have much lower airflow through the drum. Also, there is no airtight seal between drum and front, so you may essentially be sucking air through the bottom intake up past the drum and front plate.
The black-colored air flow was my concern. However, I did measure the air temperature at the bean drop port/return air duck to the squirrel cage fan. I can see clearly temperature ramping up by increase the air flow (all the way up to F9), if the tap mod is in place. That proves the heated air from the back of drum is contributing primarily.
And without the tap mod, we all know that the higher fan cause very abrupt temperature drop in the drum, which is due to the cooling air going into the drum from the “intake” without any heating at all.
So it is all about the fluidic resistance. I wish the bullet has slightly larger air-gap between drum and the metal casing inside or larger front intake port, so that this type concern can be eliminated. Still even with the current design, I think there is still plenty of air flow with tap mode.
Before tape mod, increase fan is purely like just a heating brake, like putting a brake on the heating, which I consider a lesser form of roasting error mitigation. So I used no more than F4 and only used it after 1C. I cannot use that air to roast.
Now with the tape mode, I can really use fan at much larger range to increase the heating via hot air, or slow it down by not heating that much, instead of pouring cold air to brake the heating.
Please correct me if I am wrong. But as I understand inductive heating theory, the induction elements in the Bullet do not generate heat to heat air or the drum. Instead, they generate electromagnetic radiation that creates eddy/electrical currents in the drum’s conductive material which in turn causes the metal to become hot. So air passing under the drum would also draw heat and cool the drum before reentering the drum at the rear for a zero net effect. So no different than drawing air from the rear of the drum. No?
Drawing thermal energy from the drum to air is exactly the goal. With this capability, now you can decide to roast the beans via heated drum surface (conductive heating) or via heated air (convective heating). There is certainly radiative heating involved, but let’s not worry about for the simplicity.
So by sending more air to be heated by the hot drum surface as it rubs through the thin gap of the entire length outside of the drum, now you can move the thermal energy from drum to hot air and the roasting is tilted more toward the convective heating. On the other hand, use less fan/air the beans are mainly roasted via conductive heating. That is the purpose of this mod. The extreme example are the fluidic-bed roaster, such as Fresh Roast 800, or air popcorn machine. They heat purely by heated air.
In gas heated roasted, the air can be heated much more effectively and to a much higher temperature, so the switching of conductive and convective heating is even more effective and apparent. For the inductive heated Bullet, the air is unfortunately limited by the drum temperature, so the effect is not as pronounce as the gas-heated roaster. It is the recognized limitation on that regard, but the tape mod can improve the effectiveness at least to the upper limit of Bullet’s design.
Without tape mod, the fan basically drawing cold air into the drum. The purpose of the air flow is reduced to removing moisture and chaff, and sometimes it serves as damper to the heating efficiency. As you can imagine, by taking thermal energy out of drum this design would be fine for the moderate to slow roasting, but it will limit the possibility of achieving faster and high-RoR roasting. Again, it is fine for some people, and yet not ideal for others.
@puckja - Quite a few of us in this forum are not on FB, would you be kind enough to post picture(s) of what this tape mod looks like? Thanks in advance.
Here is the the FB post:
Tape Mod:
Some people asked about the modification to raise the influx air temperature. I could share what I did with the disclaimer. This change is only for my own experiment and not suggesting the general public to follow. If you do any of these changes, you take your own responsibility and risk.
So the changes I made is simply using three aluminum tapes (for fire proof and thermal stability purpose) to block the "curved holes around the drum shaft, as it is shown in the graph. Now the strong cold air pushed out by the “PCB fan” (and ANOTER PCB fan inside the PCB circuit assembly) will not enter the drum but vented out through two arrays of holes on the plastic shell. One set of holes is on the chaff box we cleaned every time.
The net effect is shown at the 2nd picture, to block the cold air (blue dashed line) into the drum.
And please do share your experience if you do the similar change. I did two small-batch trials so far and they both finished normally without any issues. I did notice the increased thermal energy in the roast due the lack of outside cooling air.
Image 1: shows the air flow without tape mode and the measured temperature (114F) at the intake. The heated air with tape mod can achieve 180F when the drum was heated to 300F in a quick test. Note: the red-dashed line are hot air rubbing between the drum and the metal shell of Bullet. Blue-dashed line are the cold air OUTSIDE of shell inside the heating coil and electronic box. This cold air will be slightly warmed up by the thermal waste of the electronics and pushed out into the narrow chamber between chaff collection box and the rear panel of Bullet. In the original design, such lukewarm air (about 114F) is drawn into the drum. With tape mod, it will be blocked and pushed out through the side holes on the plastic shell.
Image 2: tape mod location, and the new cold air flow path (not going into intake but exit from the side holes
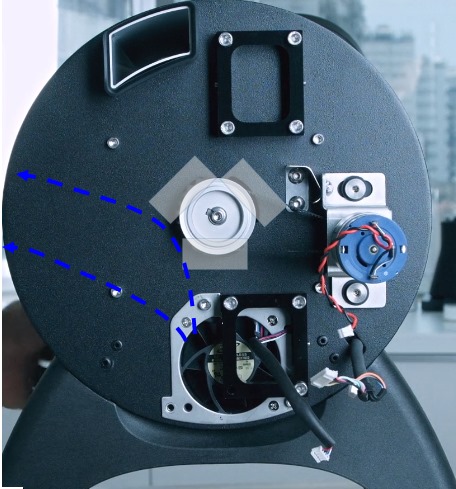
Thank you! At least now we can follow what you’re referencing